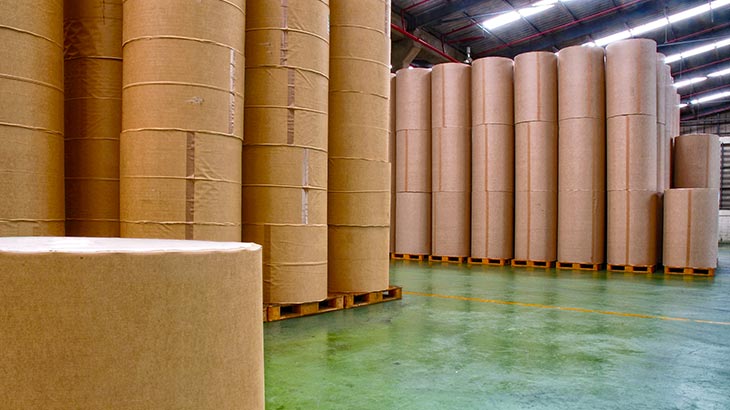
Background
With paper mill operations dating back to 1852, the mill that houses the White Mountain Paper facility has been producing paper products in the state of New Hampshire for well over 160 years. A building of this age, however, demands maintenance. The paper mill has changed hands several times over the course of its tenure. In 2020, the previous company filed for bankruptcy after struggling with its operations and deferring maintenance of the facility for years. Under new ownership, the Mill’s assets were acquired at the end of 2020 and the now White Mountain Paper Company underwent an examination of its infrastructure in order to improve efficiency and increase stability to support production for decades to come.
Challenge
Years of deferred maintenance and lack of investment by prior ownerships resulted in two primary challenges faced by the White Mountain Paper team. The existing lighting system had multiple failures; it was deemed end-of-life and could no longer adequately support the manufacturing processes, basic visibility and overall safety requirements needed at the paper mill. The mill also operated with a single air compressor that had been in use for almost 10 years and was originally purchased used. An unreliable and inefficient piece of equipment, the air compressor put the whole mill at risk for unscheduled downtime, ran on oil, and barely generated sufficient airflow for current operations.
Solution
After the acquisition, White Mountain Paper’s management team took a serious look at modernizing the plant, addressing deferred maintenance and reducing their overall energy consumption. As a NHSaves® utility partner, Eversource stepped in to help connect the paper mill with the right resources, expertise and incentive programs available to support their needs.
The mill first replaced their outdated lighting with LEDs. After evaluating a few vendors recommended by Eversource, White Mountain Paper selected Energy Management Consultants (EMC), a long-time partner in the NHSaves programs. The modern-day lighting upgrades gave employees a safer, brighter place to work and offered a visual representation of the kind of investment leadership at the mill was willing to make to create a better working environment.
For the air compressor project, the mill worked with a partner that Eversource had also been collaborating with for several years: Compressor Energy Services (CES). CES researched various system leaks and worked with White Mountain Paper’s ownership and management and recommended a full replacement to address various system leaks. The CES and White Mountain Paper teams worked with our Eversource Energy Efficiency Consultant on the project to select and install two 160 kW Atlas Copco variable speed compressors. The two systems mean one is always available for back-up in the event of required maintenance or system failure and will allow for future growth.
When Eversource first engaged with the mill, their compressed air system was operating at the lower end of the efficiency scale. Now, White Mountain Paper is operating with one of the most efficient compressed air systems available.
“We’re proud to highlight these energy efficiency upgrades in the White Mountain Paper mill. The LED lighting project has been a real ‘bright spot’ and Eversource has been such a great partner to help us move forward, making the mill more efficient and what it should be today.” Claudia Hunt, Vice President of Finance, White Mountain Paper
Results Summary
The White Mountain Paper team experienced several major results from these initiatives. The new LED lighting provided immediate and significant visibility improvements to the space. Prior to this project, there were parts of the mill that had never had lighting previously installed. This project also resulted in the most savings of any single lighting project incentivized under the NHSaves program to date.
Additionally, the air compressor project immediately mitigated the risk of downtime, which could be extensive, impact production and drive up costs. The back-up air compressor and high efficiency of the new equipment made this investment a clear choice for the White Mountain Paper team.
Together, these measures reduced the mill’s overall power consumption by approximately 60%.
The upgrades resulted in cost efficiency, as well as energy efficiency benefits that help preserve the mill’s operations and associated 75+ jobs, keeping them secure and creating opportunities for future growth. Randy Rand, Advisor and acting Operations Manager for White Mountain Paper said, “The relationship between White Mountain Paper and Eversource has been key in achieving our efficiency goals.”
Annual estimated kWh savings: 3,934,577
Lifetime estimated kWh savings: 56,999,876
Total Incentive: $660,800
Annual estimated cost savings: $26,000-$29,000