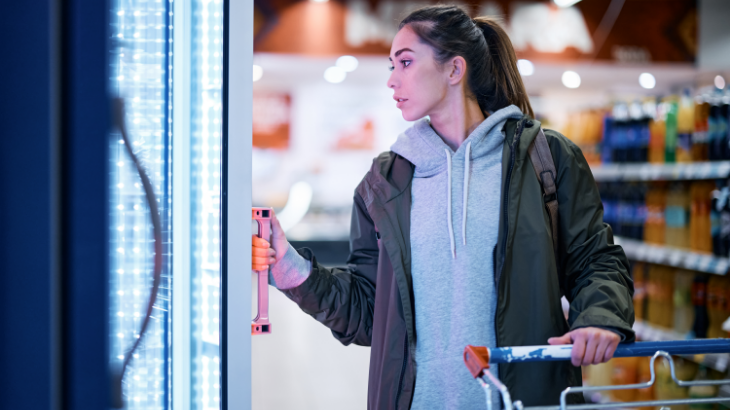
Key Points
- Refrigeration controls save energy by matching equipment operations to system needs.
- System components run more efficiently, based on input from sensors and control instructions.
- Controls not only save energy, they also help to reduce demand charges and extend equipment life.
How refrigeration controls work Refrigeration systems are critical to a wide variety of industries, but they use a substantial amount of energy. Intelligent controls reduce energy costs by matching component operations to the actual needs of the system. In addition, controls can reduce equipment wear, extending operating life and lowering repair costs.
Refrigeration controls use sensors and embedded control algorithms or instructions to run system components efficiently. Major system components include compressors, condensers, evaporators, pumps and fans. Components respond to input from sensors and vary their operation based on control instructions. Control devices minimize the simultaneous operation of individual refrigeration components to reduce peak demand. Coordinating refrigeration controls with other high-energy use equipment, such as large motors or conveyors, can improve your facility load profile substantially, saving on energy costs.
Control strategies
A variety of methods and technologies are available to control refrigeration system energy use, including the following:
- Variable frequency drives (VFD). Fan motors often waste energy by running at full speed, even during periods of peak demand. Variable speed technology uses sensors to operate fans only at the speed required, reducing the need to start and stop motors. In addition to energy savings, VFDs reduce equipment wear and improve product quality by minimizing variation in operating temperature.
- Demand refrigeration and defrost cycles. Demand controls shut down the refrigeration system—or parts of it—at a set temperature, returning it to operation only when rising temperatures require refrigeration. A demand defrost cycle uses sensors to measure the temperature of the evaporator surface, as well as frost accumulation and humidity. These measurements help to determine if a defrost cycle should be initiated.
- Load shedding. Load shedding reduces energy consumption and peak demand charges by turning off or delaying the start of equipment if it is not needed immediately. Sensors measure electrical activity throughout the system and shut down or delay machines selectively when activity reaches a set point.
- Anti-sweat heater controls. Anti-sweat heaters minimize condensation and typically operate at full power at all times. Controls save energy by matching the heater use with condensation levels. Humidity sensors located in the refrigerator or freezer signal the controller to adjust power flow to the heaters.
- Floating head pressure. Refrigeration systems commonly use fixed head pressure control, in which condensing pressure is maintained by a condenser fan, regardless of the system load. Allowing the pressure to vary or float based on outdoor conditions helps to improve system efficiency, while extending equipment life.
Selecting the right control strategy depends on your application and control needs. For example, demand refrigeration or load shedding can help lower demand charges, while VFDs can reduce energy consumption and create a more uniform operating temperature. Consult your system supplier to find out which control method would best suit your requirements.