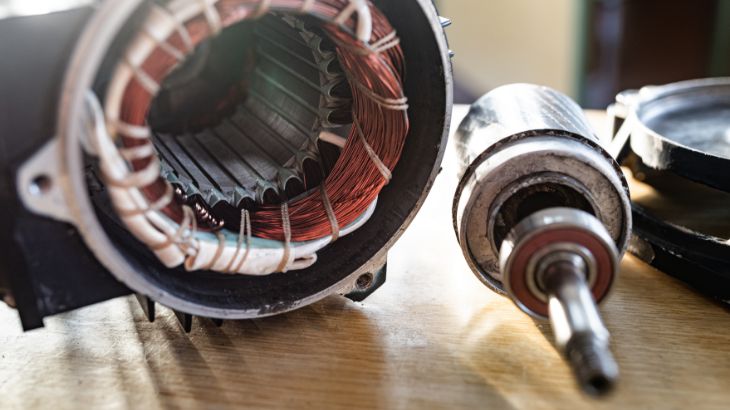
Key Points
- An effective motor policy can save money on repair and replacement, and improve your productivity.
- Planning is essential. Start with an inventory of all equipment and a list of trusted suppliers.
- Include replacement guidelines and repair specifications, as well as preventive maintenance.
Motors are critical to operations and they make up half of the electricity used in many facilities. An effective motor policy can save money and improve your productivity. The ultimate goal of a motor policy is to minimize utility and repair costs, as well as downtime. Major components include replacement guidelines, repair specifications and a maintenance program. Regulatory changes also need to be taken into consideration since they improve the economics of replacement motors.
Start with a plan
Any successful policy begins with planning. The following steps will help ensure that you have the information necessary to optimize motor systems:
- Inventory all equipment with identification numbers, nameplate information and hours of operation.
- Develop a motor replacement plan for all equipment. Include supplier information, as well as details about replacement type (new versus rebuilt).
- Set guidelines for proper disposal of all discarded equipment and update regularly to ensure compliance with environmental regulations.
- Maintain a list of trusted suppliers for each type of motor in inventory.
- Make sure all newly purchased motors meet federal energy-efficiency regulations.
Replacement guidelines
Keep long-term goals in mind when making replacement decisions. Consider the age of the motor, its condition and the availability of similar equipment. These standards provide guidance for effective decision making:
- Verify that motors are sized properly. Oversized units are candidates for replacement.
- Compare the efficiency of existing motors to energy-efficiency standards. Operating costs are a significant factor, and the efficiency gains of a new motor may warrant replacement.
- Motors that are 50 to 100 horsepower (hp) or larger with an annual operating time of less than 4,000 hours can be rewound if core iron specifications are acceptable.
- Motors should be rewound a maximum of three times.
- Replace motors if the cost repair costs exceed 60 percent of the cost of replacement.
- Before replacing motors at your facility, contact your Eversource Account Executive to determine if there are incentives available to help you make the switch.
Repair specifications
If the decision is made to repair a motor, the following procedures can help ensure quality and reduce overall costs:
- Detail procedures for dismantling, inspection, testing and reassembly of specific motors.
- Develop a set of motor rebuilding standards.
- Establish a set of procedures to test repaired or rebuilt motors.
- Repair motors to their original design regarding turns, winding, configuration and other specifications.
Repair specifications should be well-designed and consistently applied to minimize any loss in efficiency or performance.
Establishing a maintenance program
Preventive maintenance is essential to realizing motor policy goals. The following checklist of maintenance practices will help improve motor performance and save you money on repair and replacement costs.